



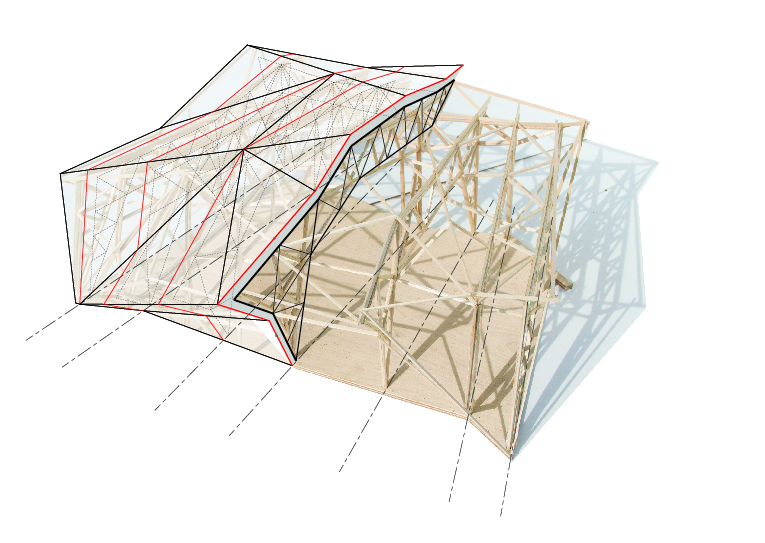
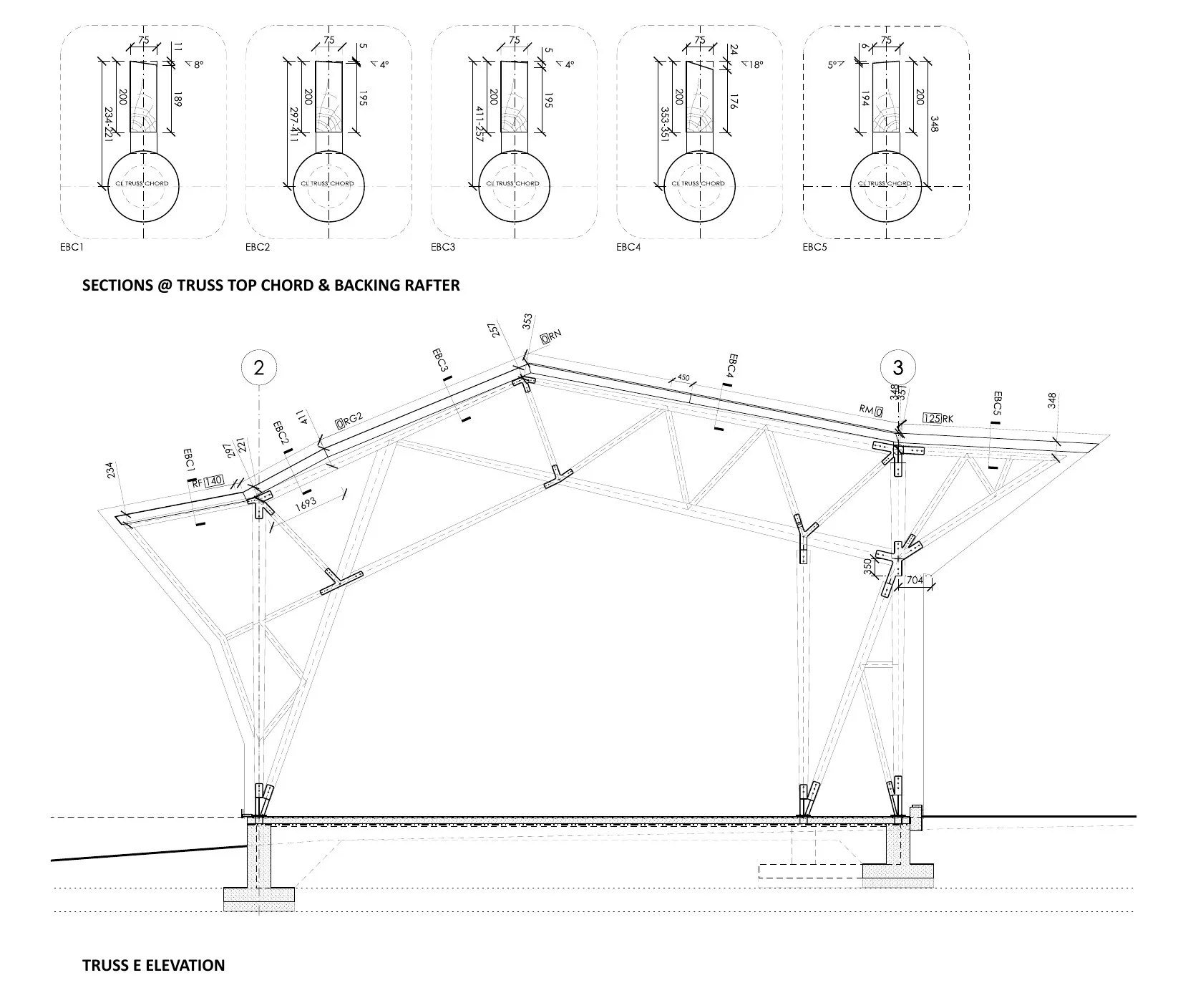

Architectural Association Master of Architecture Course Design & Make Project 2010-2012
Project Credits
Students: Nozomi Nakabayashi (Design & Make); Elena Gaider, Eyal Shaviv, Olivia Putihrai, Samuel Nelson, Sanem Alper (Diploma Unit 19)
Teaching Team: Martin Self (Program Director); Piers Taylor, Kate Darby (Studio Tutors); Charley Brentnall (Make Tutor)
Executive Architect: Mitchell Taylor Workshop (Piers Taylor, Luke Holcombe)
Structural Engineer: Atelier One (Aran Chadwick, Luis Fernandez, Elizabeth Bismut, Eva MacNamara)
Civil Engineer: Buro Happold (Bob Riley, Joseph Walton)
Contractor: Charley Brentnall
Timber Testing: Bath University (Prof Richard Harris, Nick Gathercole)
Photo by Valerie Bennett

The ‘Big Shed’ is a 500 m2 Assembly Workshop completed in 2012. It functions as the central workspace at Hooke Park, Architectural Association’s Woodland campus in Dorset, UK. As a part of my Design and Make Master of Architecture project, I was involved in the project as the lead student architect working through to the final construction phase.
The structure achieves a long span using planer timber trusses constructed from small-diameter conifer roundwood timber. The project’s key agenda was to demonstrate the structural use of forest thinning materials, which are usually not considered structural due to their small section sizes when milled to a square profile. However, using them in round retaining the fibre continuity within the timber structure, as demonstrated in the truss design of the Big Shed, optimises their tensile and compressive characteristics.

Each truss was pre-fabricated and lifted into place one by one. The cladding panels were also prefabricated as cassetts.

The design of the building volume developed through the lived experience and observation of life on site. The two main strands, the physical building experience and day-to-day living on site experience, helped clarify the practical requirements and formed the initial design brief.
The facetted building geometry was chosen to reflect the site context where each aspect, North, South, East and West, required different geometry to serve varying practical functions.
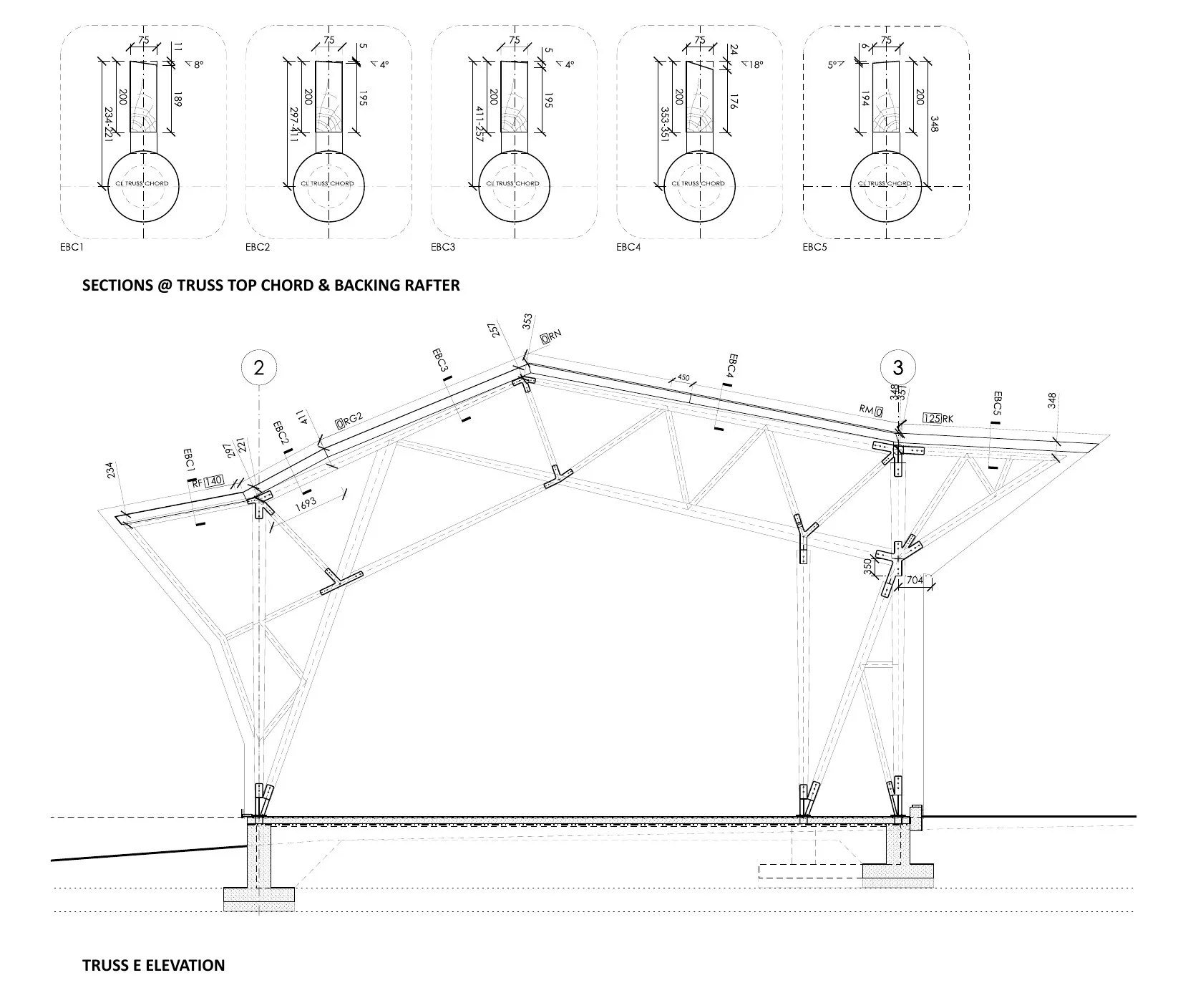
The truss structure connection has pioneered the use of high-capacity screwed connections within large round-wood trusses. This approach allows trees to be used ‘in-the-round’ in complex structures without complex steel connection plates.
The complete structure consists of 8 round larch timber trusses joined by square sawn Douglas Fir struts with cladding cassettes. of W. Red cedar, poly carbonate and tin roof.
The fabrication of the trusses was carried out by a team of students both from Design & Make and summer volunteers on the AA’s ‘SummerBuild’ programme at Hooke Park, who worked alongside experienced timber framers. Each of the planar trusses was fabricated and assembled horizontally, before all being lifted into position on the building’s concrete slab. Similarly, the cladding cassettes were assembled flat and then raised into place.